Seto 1.67 Photochrome Linsen SHMC
Spezifikation
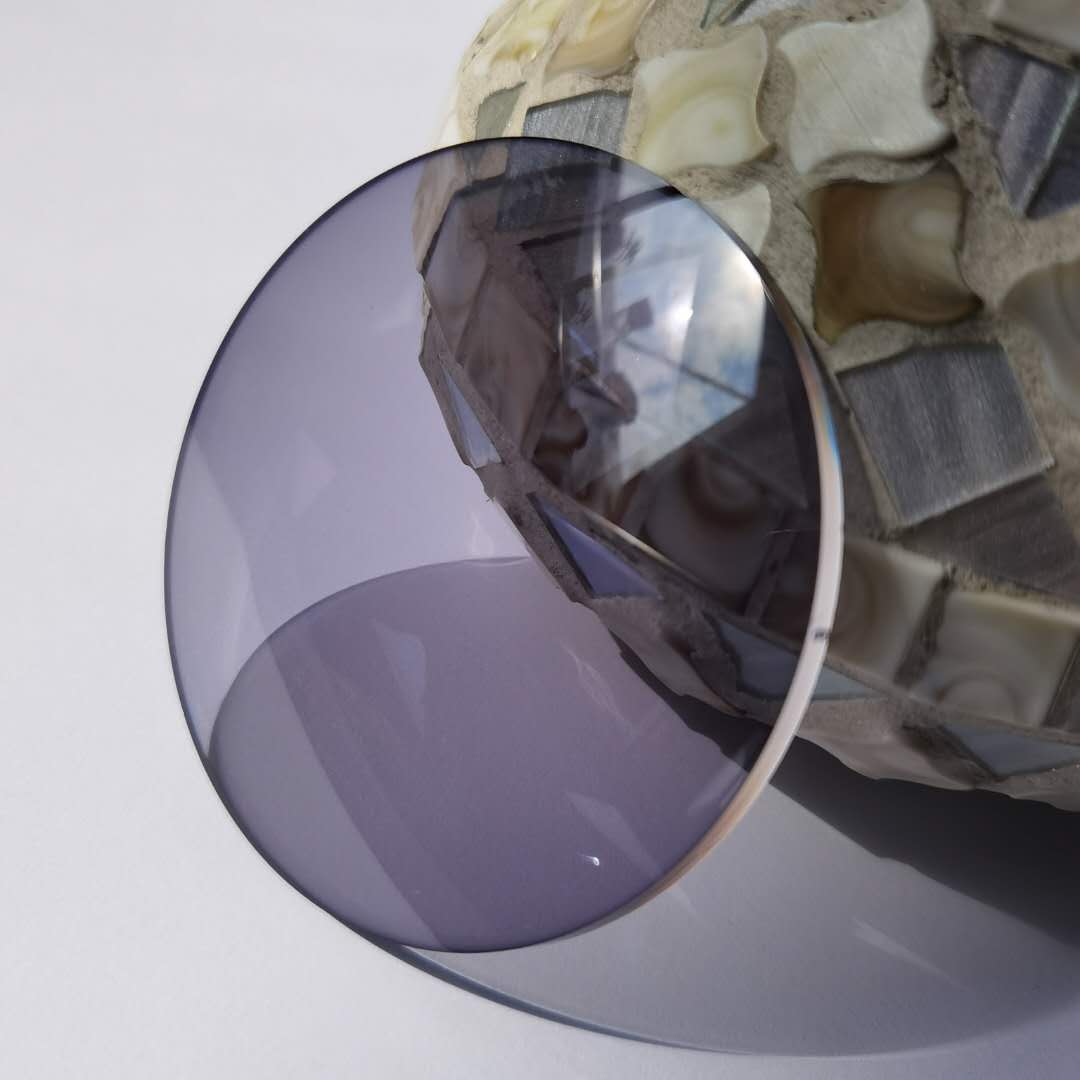
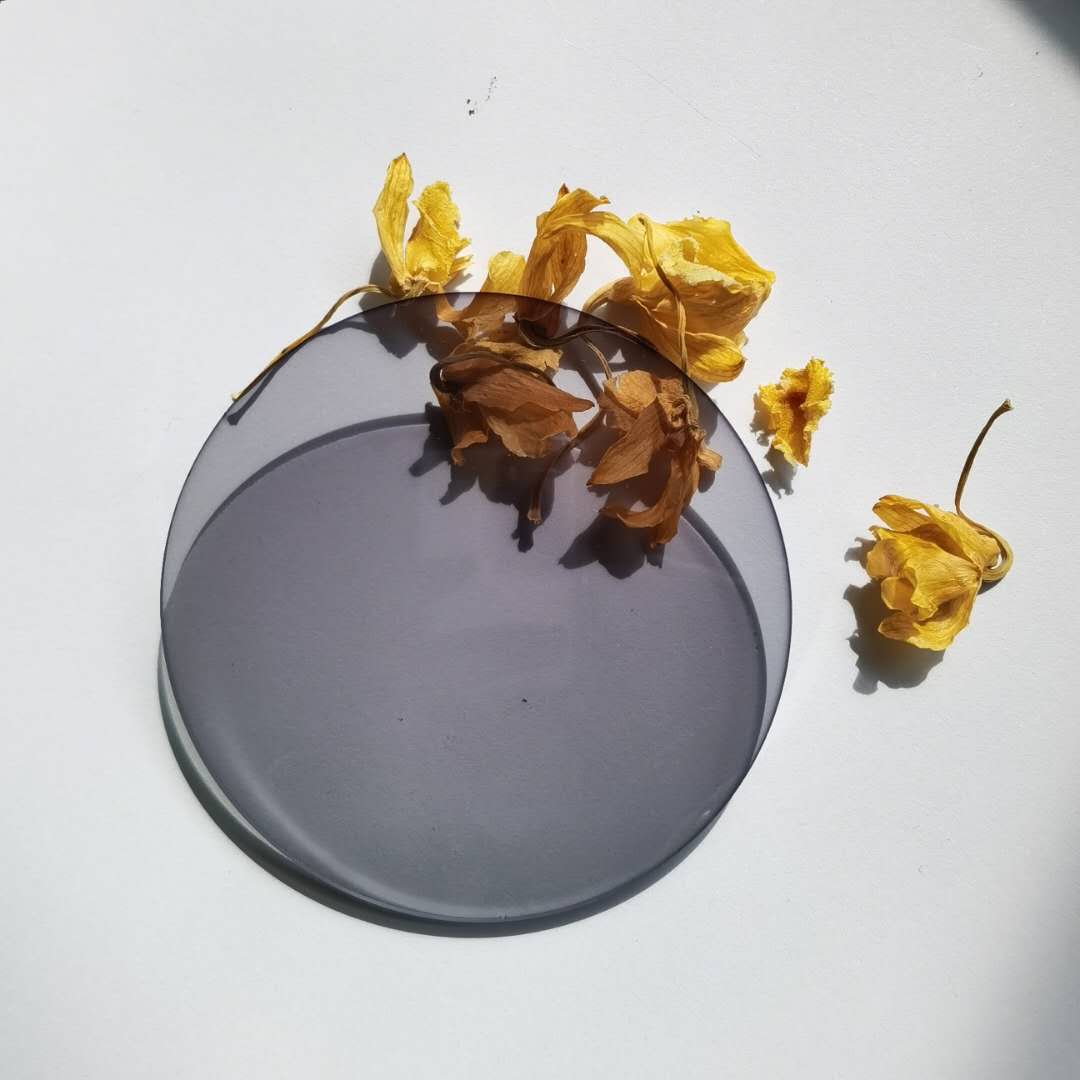
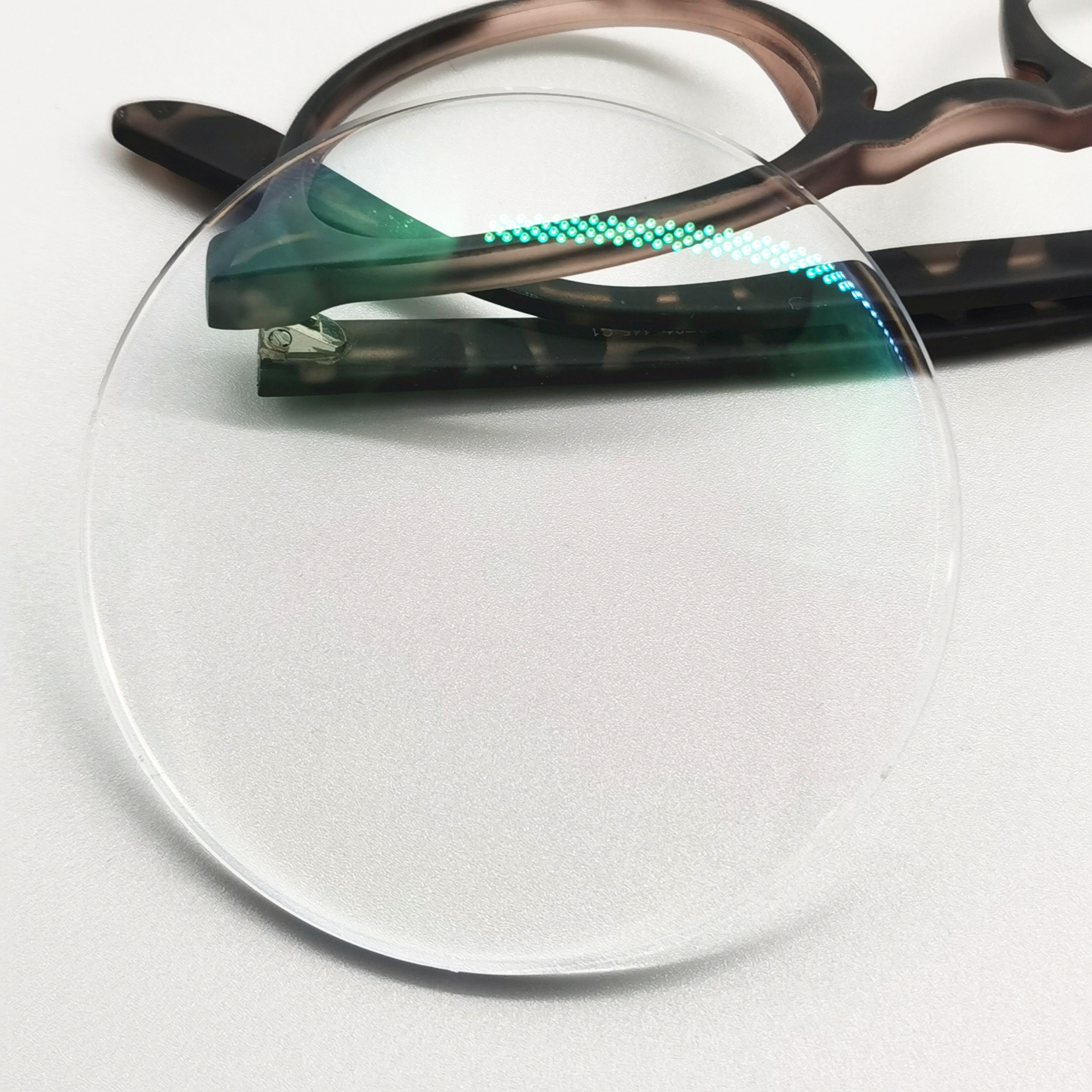
1,67 Photochrom -SHMC -optische Linse | |
Modell: | 1.67 Optisches Objektiv |
Herkunftsort: | Jiangsu, China |
Marke: | Seto |
Linsenmaterial: | Harz |
Linsen Farbe: | Klar |
Brechungsindex: | 1.67 |
Durchmesser: | 75/70/65 mm |
Funktion: | Photochrom |
ABBE -Wert: | 32 |
Spezifische Schwerkraft: | 1.35 |
Beschichtungsauswahl: | HMC/SHMC |
Beschichtungsfarbe | Grün |
Leistungsbereich: | SPH: 0,00 ~ -12,00; +0,25 ~ +6.00; Zylor: 0,00 ~ -4,00 |
Produktmerkmale
1) Was ist Spinbeschichtung?
Spinbeschichtung ist ein Verfahren, mit dem gleichmäßige Dünnfilme auf flache Substrate abgelegt werden. Normalerweise wird in der Mitte des Substrats eine kleine Menge Beschichtmaterials aufgetragen, die sich entweder mit niedriger Geschwindigkeit dreht oder überhaupt nicht dreht. Das Substrat wird dann mit einer Geschwindigkeit von bis zu 10.000 U / min gedreht, um das Beschichtungsmaterial durch Zentrifugalkraft zu verteilen. Eine für die Spinbeschichtung verwendete Maschine wird als Spin -Coater oder einfach Spinner bezeichnet.
Die Rotation wird fortgesetzt, während sich die Flüssigkeit von den Rändern des Substrats abdreht, bis die gewünschte Dicke des Films erreicht ist. Das angelegte Lösungsmittel ist normalerweise volatil und verdunstet gleichzeitig. Je höher die Winkelgeschwindigkeit des Spinnens ist, desto dünner der Film. Die Dicke des Films hängt auch von der Viskosität und Konzentration der Lösung und dem Lösungsmittel ab. Pionierarbeit theoretische Analyse der Spinbeschichtung wurde von Emslie et al. Durch Universelle Beschreibung zur Vorhersage der abgelagerten Filmdicke).
Die Spinbeschichtung wird bei der Mikrofabrikation von funktionellen Oxidschichten auf Glas- oder Einkristallsubstraten unter Verwendung von Sol-Gel-Vorläufern häufig verwendet, wo sie verwendet werden können, um gleichmäßige Dünnfilme mit nanoskaligen Dicken zu erzeugen. [6] Es wird intensiv in der Photolithographie eingesetzt, um die Photoresistschichten etwa 1 Mikrometer dick abzulegen. Photoresist ist in der Regel 30 bis 60 Sekunden bei 20 bis 80 Revolutionen pro Sekunde gedreht. Es wird auch häufig für die Herstellung von planaren photonischen Strukturen aus Polymeren verwendet.
Ein Vorteil, um die Dünnfilme von Beschichtung zu spinnen, ist die Gleichmäßigkeit der Filmdicke. Aufgrund der Selbstniveau variieren die Dicken nicht mehr als 1%. Dicke Filme von Polymeren und Photoresistern können jedoch zu relativ großen Kantenperlen führen, deren Planarisation physikalische Grenzwerte aufweist.
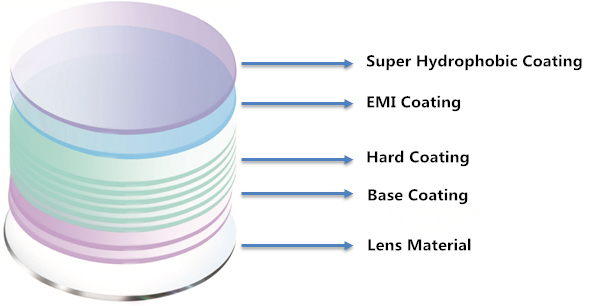
2. Klassifizierung und Prinzip der photochromen Linse
Die photochromen Linse nach den Teilen der Linsenverfärbung werden in photochromische Linsen (als "Basisänderung" bezeichnet) und die Verfärbungslinse der Membranzschicht (als "Filmänderung" bezeichnet) zwei Arten unterteilt.
Die substrat photochrome Linse wird eine chemische Substanz von Silberhalogenid im Objektivsubstrat zugesetzt. Durch die ionische Reaktion von Silberhalogenid wird es in Silber und Halogenid zersetzt, um die Linse unter starker Lichtstimulation zu färben. Nachdem das Licht schwach geworden ist, wird es zu Silberhalogenid kombiniert, sodass die Farbe leichter wird. Diese Technik wird häufig für Glasphotochroimc -Objektive verwendet.
Die Filmänderung wird speziell im Objektivbeschichtungsprozess behandelt. Zum Beispiel werden Spiropyranverbindungen für die Hochgeschwindigkeitsspinbeschichtung auf der Oberfläche der Linse verwendet. Gemäß der Intensität des Lichts und des ultravioletten Lichts kann die molekulare Struktur selbst ein- und ausgeschaltet werden, um den Effekt des Durchgangs oder des Blockierens von Licht zu erreichen.
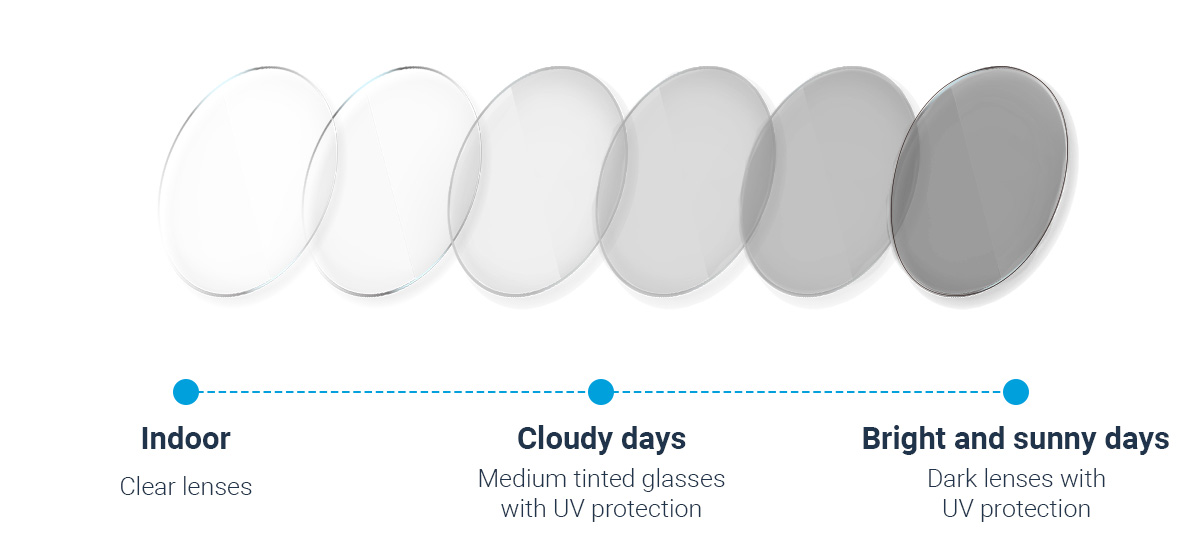
3. Beschichtungsauswahl?
Als 1,67 Photochromlinse ist die superhydrophobe Beschichtung die einzige Beschichtungswahl dafür.
Super hydrophobe Beschichtung nennt auch Crazil Coating, kann die Linsen wasserdicht, antistatisch, Anti -Schlupf und Ölresistenz machen.
Im Allgemeinen kann eine superhydrophobe Beschichtung 6 bis 12 Monate bestehen.
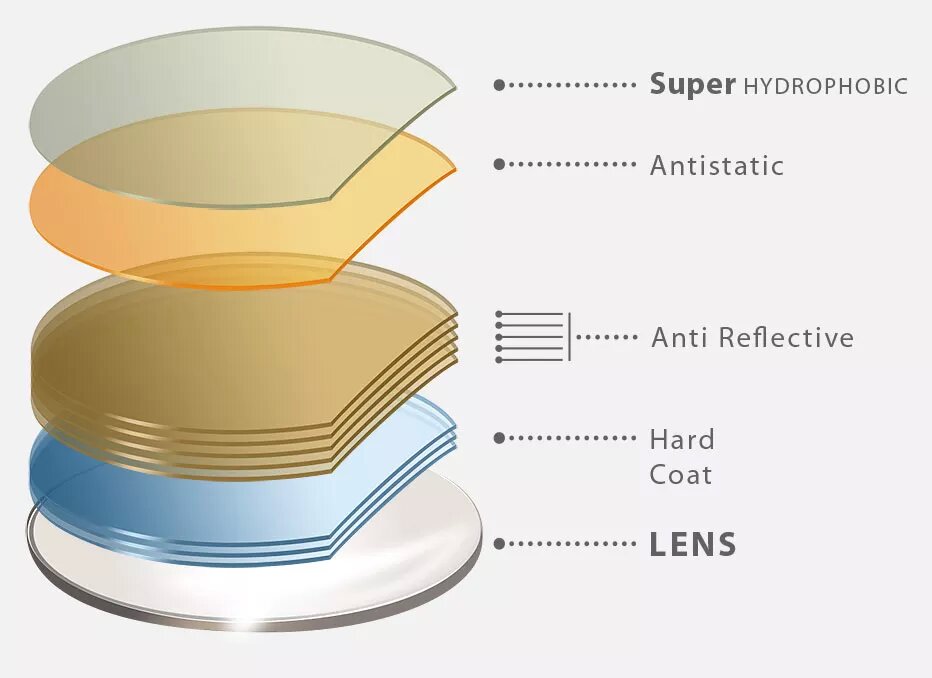
Zertifizierung
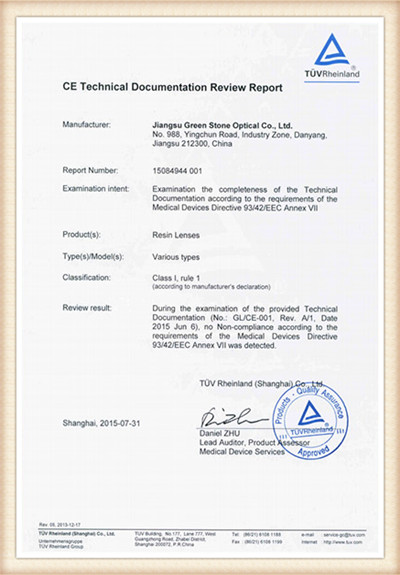
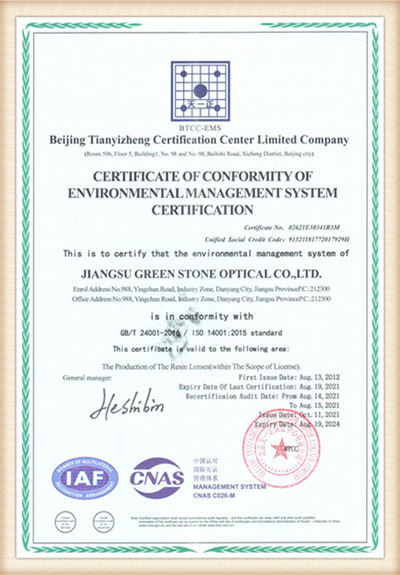
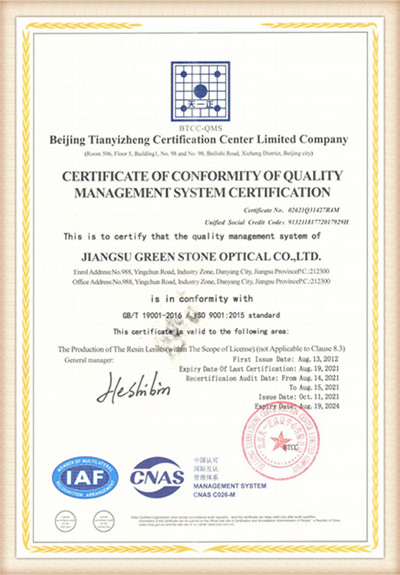
Unsere Fabrik
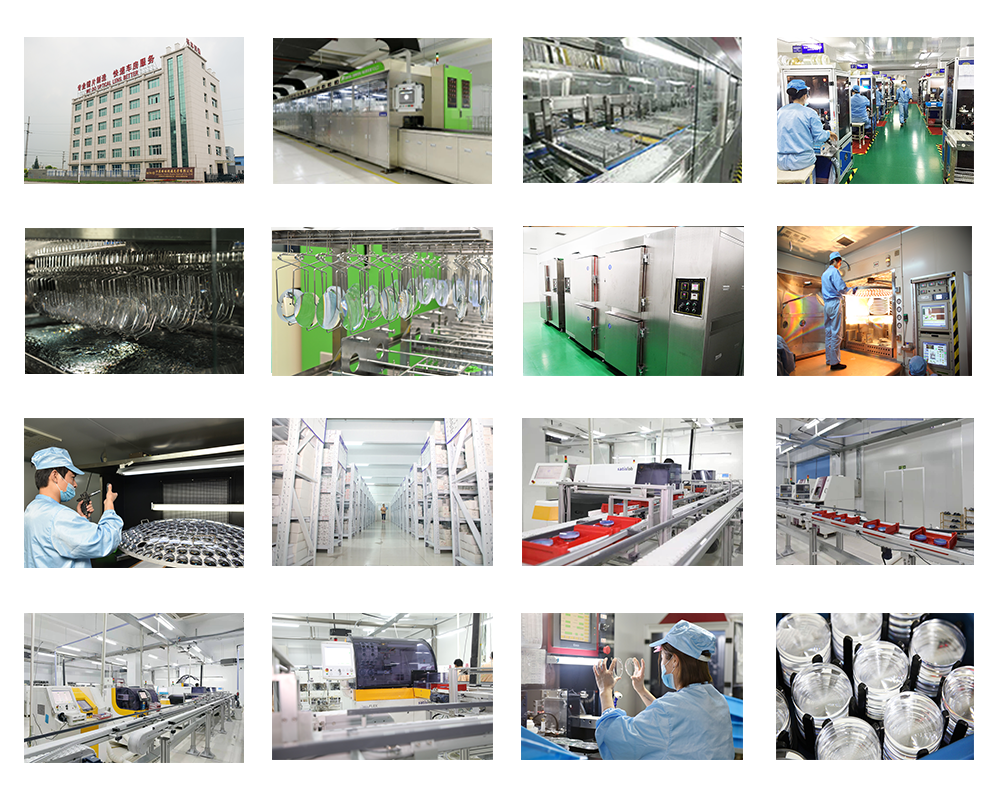